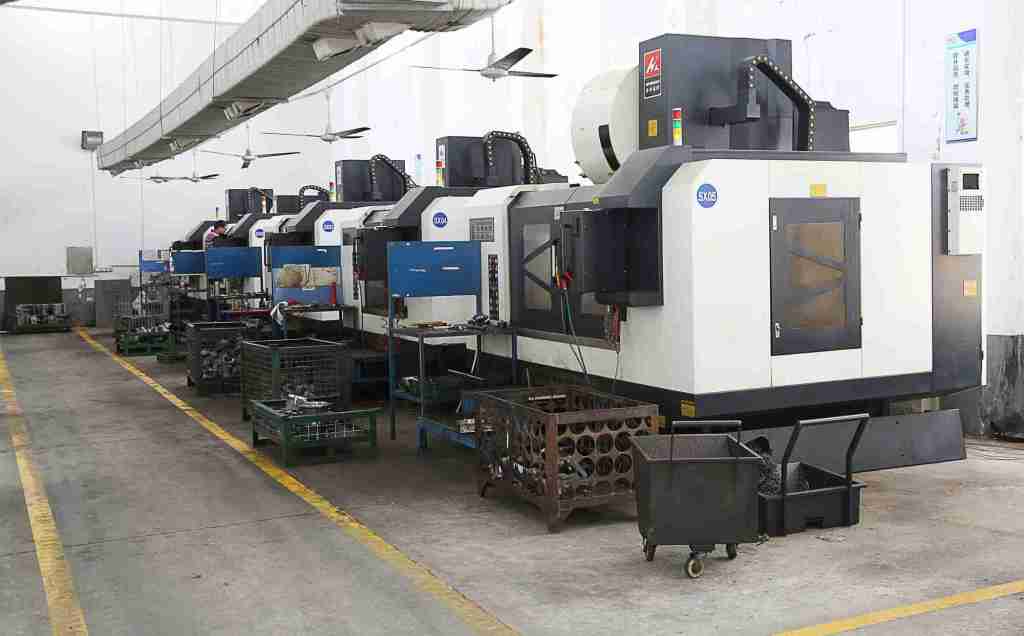
CNC (Computer Numerical Control) machining is a modern manufacturing process that utilizes computerized software and machinery to create highly precise and accurate parts from a variety of materials. It has become a prevalent method in the manufacturing industry due to its ability to produce complex and intricate parts with minimal human intervention, resulting in higher efficiency and consistency in production.
Technical Parameters:
The CNC machining process begins with a computer-aided design (CAD) model of the desired part, which is then converted into a CNC program that the machine follows to produce the final product. The machine operates on three main axes – X, Y, and Z, which move in parallel to create the desired shape and features. In some cases, a fourth axis can also be incorporated for additional movement and precision. CNC machining offers high precision and accuracy, with tolerances as low as 0.001 inches, ensuring consistency in the produced parts.
Production Characteristics:
One of the primary advantages of CNC machining is its versatility in producing parts from various materials. This includes metals such as aluminum, steel, titanium, brass, and copper, as well as plastics, wood, and composites. It can also handle both small and large batch sizes, making it suitable for both prototyping and mass production. The process also allows for multiple operations to be completed in a single setup, saving time and increasing efficiency. Additionally, the flexibility of CNC machines allows for complex shapes and features to be produced without the need for specialized tools, resulting in cost savings for manufacturers.
CNC machining is a highly automated process, which reduces the need for manpower and increases efficiency. With the use of advanced software, the process can run continuously, resulting in faster production times and shorter lead times for customers. Moreover, the precision and accuracy of CNC machining reduce the chances of errors and rework, minimizing material waste and ultimately reducing costs for the manufacturer.
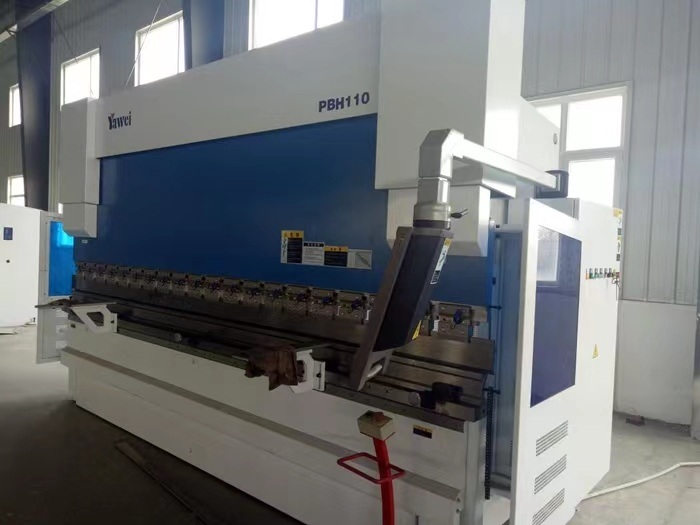
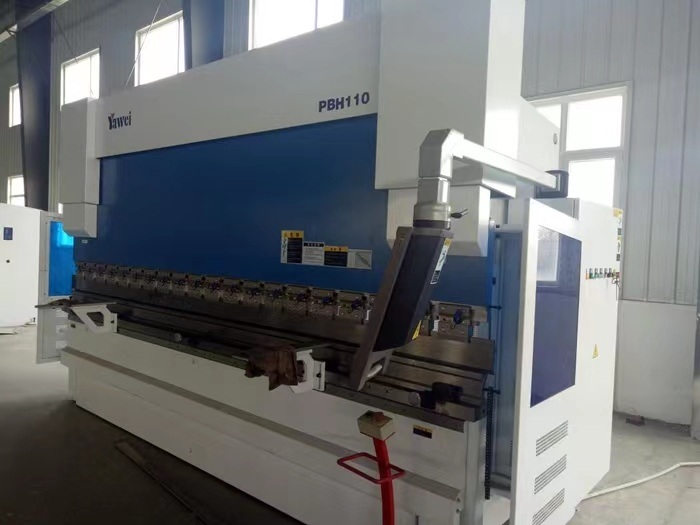
Benefits of CNC Machining:
1. High Precision and Accuracy: CNC machines are programmed to perform precise movements repeatedly, resulting in highly accurate and consistent parts. This level of precision is not achievable with manual machining methods.
2. Increased Efficiency: The use of CNC machines reduces the need for human intervention, resulting in faster production times, increased productivity, and lower labor costs for manufacturers.
3. Versatility: CNC machines can produce parts from a wide range of materials, including metals, plastics, and composites, making it suitable for a variety of industries such as automotive, aerospace, medical, and consumer electronics.
4. Cost-Effective: While the initial investment in CNC machines may be higher compared to traditional methods, the long-term cost savings from reduced labor, material waste, and faster production times make it a cost-effective solution for manufacturers.
5. Complex Parts: CNC machining allows for the production of complex shapes and features that would be difficult or impossible to achieve with traditional methods. This results in more design freedom for engineers and opens up possibilities for innovative solutions.
Challenges of CNC Machining:
1. High Initial Investment: The cost of CNC machines can be a barrier for small businesses and startups, as they can be expensive to purchase and maintain. This may limit the accessibility of CNC machining to some manufacturers.
2. Skilled Labor Requirement: While CNC machining reduces the need for manual labor, it does require skilled operators to program and operate the machines accurately. This can be a challenge for manufacturers to find and retain qualified personnel.
3. Regular Maintenance: CNC machines require regular maintenance and upkeep to ensure their accuracy and efficiency. This includes calibration, tooling, and software updates, which can add to the overall cost of production.